Combustion
Brayton offers a unique combination of empirical design codes based on over 30 years of design experience, state-of-the-art CFD simulation, and in-house testing.
Brayton’s team builds on the work of our staff consultant and mentor, Roy Norster, who’s pioneering work led the industry for over 40 years. Our team led the very successful NREC and Ingersoll-Rand (now Flex Energy) microturbine combustor development programs, achieving NOx and CO levels below those of any commercial gas turbine or microturbine. Recent Brayton projects have focused on advances in combustor durability and cooling, and bio-fuels combustion in gas turbines. Other projects include DLE rerating of industrial gas turbine combustors, advanced premix-lean burn gas turbine combustors, thermal reactors, and fiber burners.
Technical Expertise
- Detailed combustion modeling
- Integrated gas turbine system part-load analysis
- Specialized cooling geometries
- Practical combustor design
- Mechanical integration with engines / recuperated
- Meet CARB and EPA standards without after-treatment
- Biomass combustion
Our
Approach
- 1Advanced CFD Modeling
- 2Validated Analytical Design Tools
- 3Efficiency Targets and Inputs
- 4Detailed Design Package
- 5Manufacturing (Hard vs Soft Tooling)
- 6Testing and Verification
Combustion Test Facilities
Low Pressure Similitude testing of gas turbine combustors
- Brayton’s facility produces 7 kg/s (12,000 SCFM) at about 2 psig (114kPa) for Mach Number scaled testing of combustors up to 5 MW.
- Natural gas, diesel, bio-oil.
- Recuperated preheater for unvitiated combustion air up to 600 C.
- Preheated unvitiated air to 700 C, up to 750 psig (5.2 MPa), 2 kg/s
- Precise measurements – flow, temp, pressure, vibration, exit swirl through detailed zoning and mapping conventions.
- Full emission testing
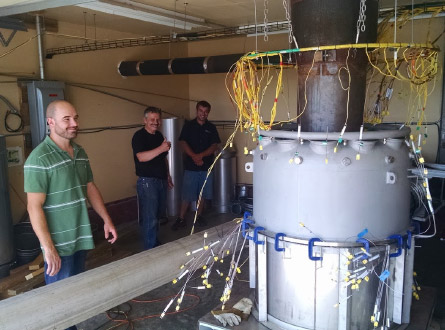
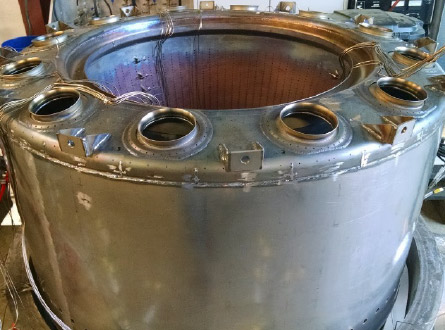
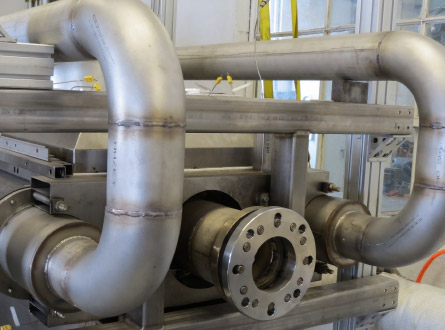