Our Facilities
Our specialized facilities have evolved around the needs of the turbomachinery industry. Our objective is to provide tools to expedite the development of new products for our clients. Brayton’s engineering and technician staff takes pride in our specialized skills to support all aspects of the product development process.
Prototyping
Brayton is equipped with a diverse range of equipment for rapid prototyping and process development – including CNC machinery, specialized welding systems and multiple fabrication tools throughout our facility.
Brayton can create or modify custom tooling and finished hardware within 5 µm tolerances to meet the most demanding accuracy requirements for turbomachinery and high-speed bearings systems. With engineers, designers, and machinists working together, Brayton’s in-house capability provides an ideal environment for rapid prototyping.
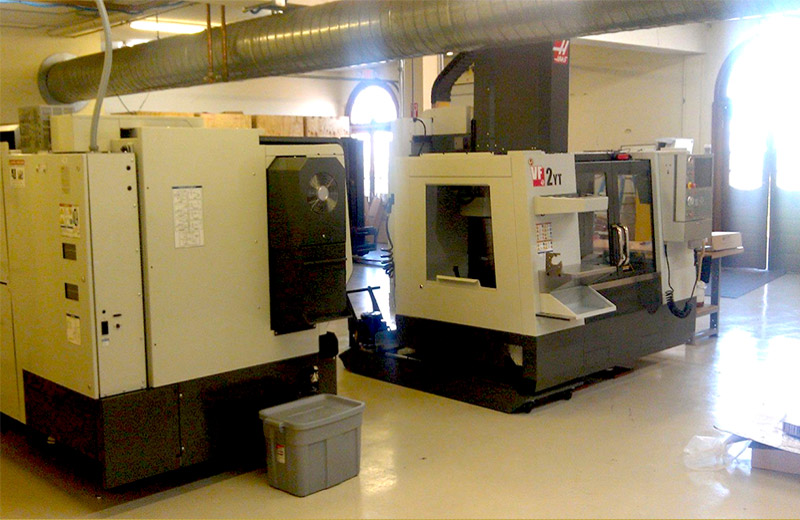
Manufacturing
Brayton’s 28,000 sq/ft facility has includes 9,000 sq/ft dedicated to heat exchanger manufacturing and pilot production . This flexible manufacturing facility is equipped with metal cleaning, braze preparation stations, micro-channel and micro-pore surface fabrication, auto-welding, vacuum brazing, and diffusion bonding. The experienced staff develops the special processes and quality assurance procedures for each gas turbine recuperators and compact heat exchangers.
As part of the manufacturing qualification process, Brayton has developed special accelerated creep and fatigue testing stations.
HEAT EXCHNAGER DESIGN AND TEST FACILITIES
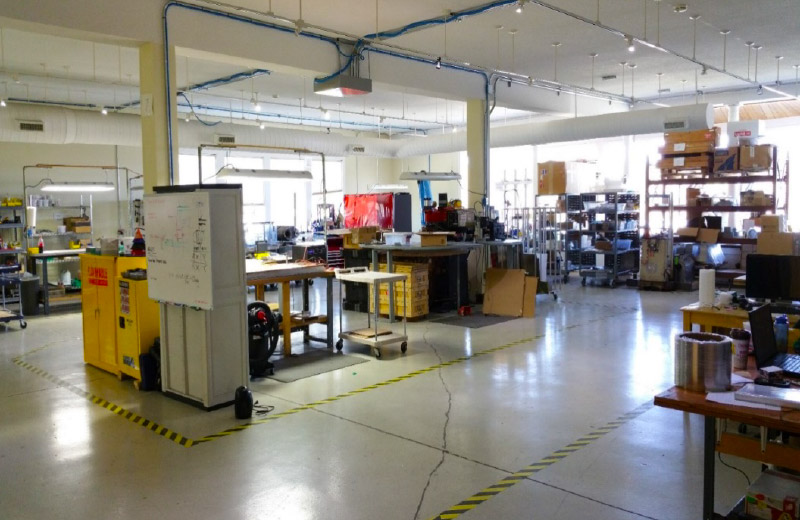
Laboratory
Brayton’s combustion gas stands are capable of full scale aerodynamic and aerodynamic similitude testing of turbines and compressors. The facility’s compressor bank delivers nominally 1 kg/s (2000 scfm) at up to 12 bar to the specialized turbomachinery test stand. The recuperated test stand and internal combustor have been qualified to 1150C / 2100 F delivery temperatures. Specialized instrumentation enables the mapping of compressors and turbines. In the installation shown on the right, special traversing cobra probes are used to measure the turbine exit flow angle from hub to shroud.
The Brayton staff offers over 30 years of turbomachinery test experience to our clients.
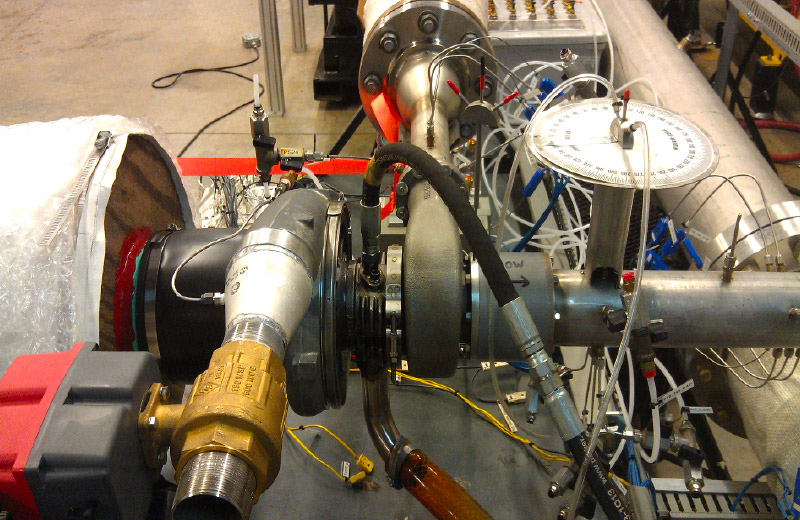
Computational Tools
Brayton Energy utilizes computational fluid dynamics to provide insight into turbines, compressors, volutes, ducting, heat exchangers, and combustion systems. We strive to validate the performance of complex aerodynamic systems with well-planned experiments, backed by rigorous testing procedures. Brayton Energy utilizes ANSYS FLUENT and CFX software, as well as Concepts NREC software in our design strategy.
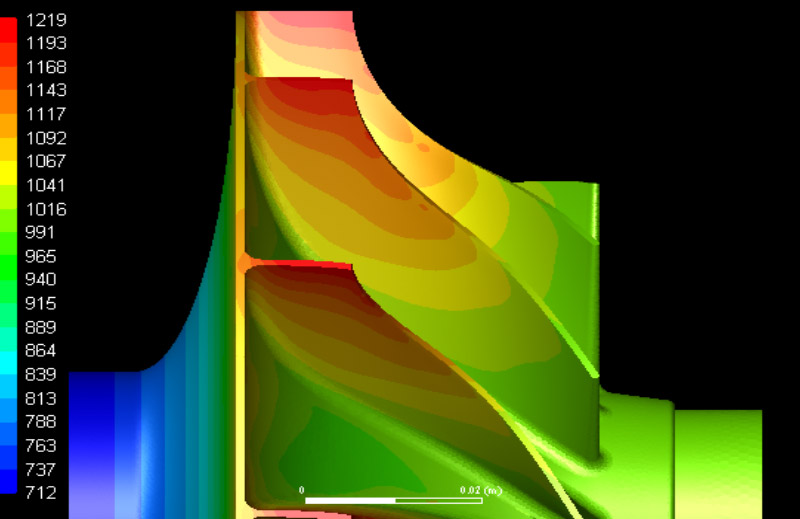