Renewable Energy
Earth offers us vast solar, biomass, and wind resources, sufficient to power civilized growth indefinitely. Brayton projects in clean burning bio-derived fuels and concentrated solar power contribute to the transition away from fossil fuels. Brayton’s development of combined solar and thermal storage has received international recognition.
Technical Expertise
Over 30 years of Concentrated solar power R&D
- CSP thermo-optical modeling
- Solar receiver design for dishes, towers, troughs
- Articulating pipe connections for molten salt transport systems
- Thermal energy storage using thermoclines, flowing particles (micro-sand) molten salt, thermochemical media, and phase change materials.
- Air-Brayton, supercritical CO2, and Stirling cycles
Biomass and digester gas-power gas turbines
- High-temp heat exchanger design for indirect combustion and waste heat recovery
- Landfill and digester gas combustion
- Biomass combustion
- Novel gas turbine solid fuel combustion
Solar Receiver Technology: Gas turbine (Air-Brayton) Cycle
Applying our microturbine and gas turbine design experience, Brayton Engineers have built and tested five Dish Brayton projects. Solar receivers operating at 1300°C have been tested, employing volumetric receivers.
Recent efforts successfully tested solar-activated compressed air energy storage, and explored advanced Brayton cycles for power towers, working under Google’s RE initiative
Solar Receiver Technology:sCO2 Brayton Cycles with Energy Storage
Continuing under a series of US DOE competitive awards since 2010, Brayton is developing the solar receiver and energy storage subsystems for the future CSP Power plant. The plant will have 4 to 8 hours of thermal storage.
Thermo-chemical, molten salt, flowing particle beds, phase change materials, and packed-bed thermocline energy storage systems have been rigorously analyzed.
Solar Design & Test Facilities
Brayton’s laboratory focuses on testing, performing thermal-mechanical testing of receivers and components.
- Solar receiver design: ray tracing, thermal analysis, CFD, FEA
- Microchannel heat exchanger manufacturing facility
- Vacuum brazing, laser welding, CNC machining
- Mil-spec Qualification of high temp heat exchangers
- Up to 100 MPa and 900C, fluids: sCO2, and air
- Solar simulator and heat exchanger performance characterization – 400 suns, (100mm x 1000mm)
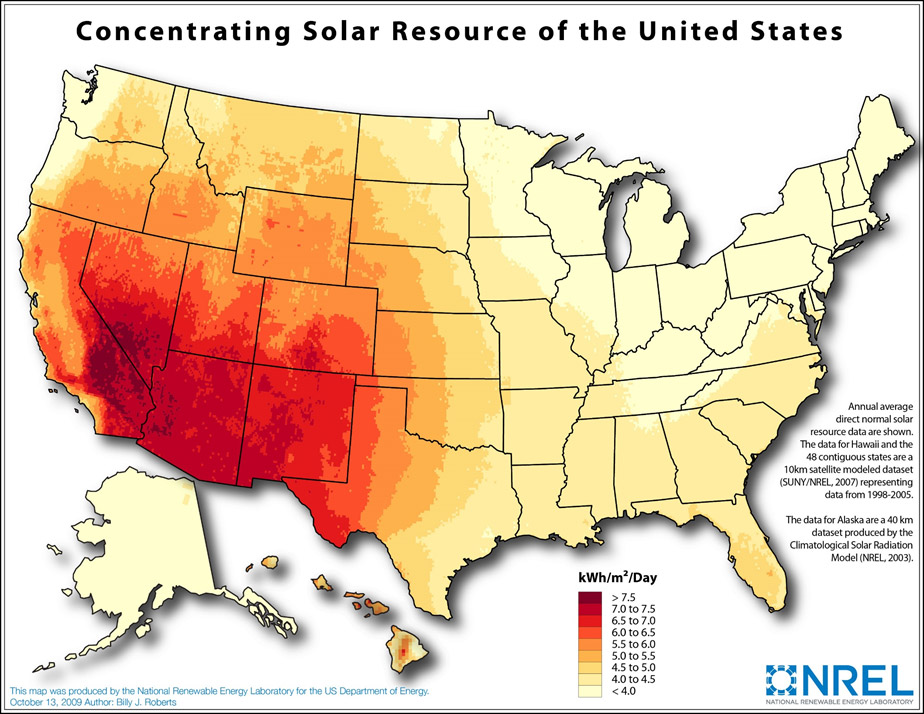
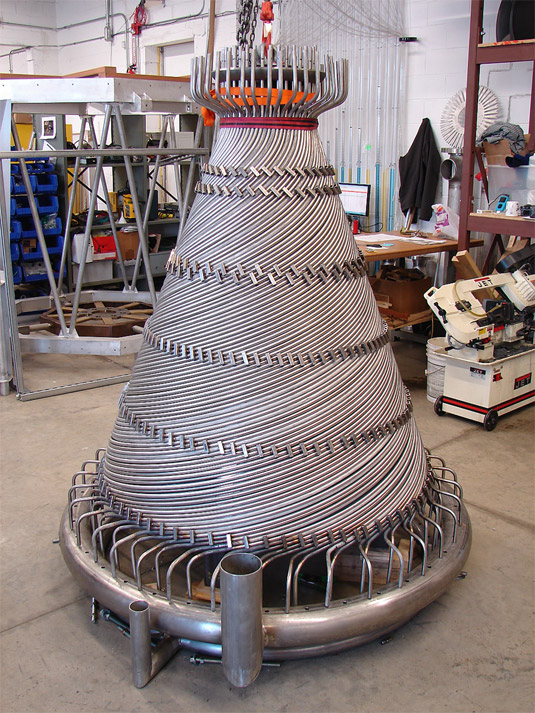
Forestry Residue
Agricultural Crop Residue
Solar